
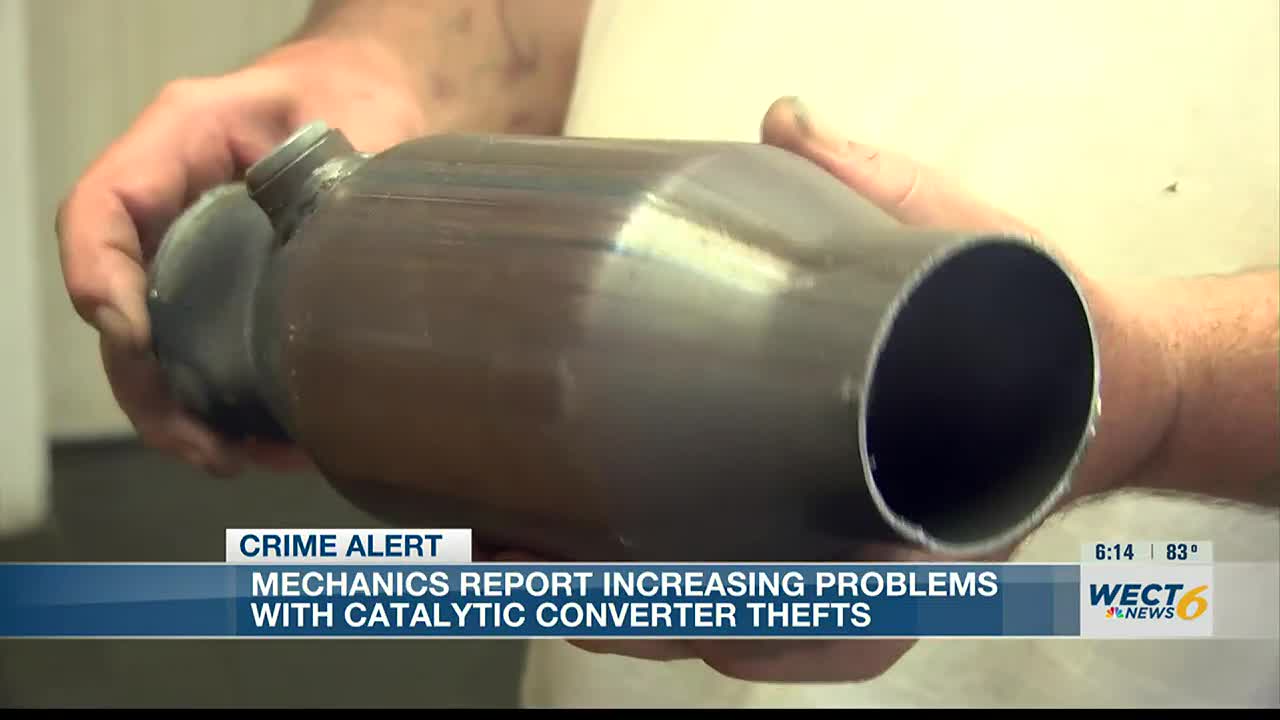
Only after the engine is started and driven, does the catalyst monitor run. Consequently, it’s very important for supplier and technician alike to meet EPA requirements by selecting the correct catalytic converter for the application. The effectiveness of the converter is basically determined by the amount of precious metals present on the honeycomb substrate. The precious metals used as catalysts are distributed in molecular form over a rough-surfaced ceramic wash coat covering the metallic honeycomb substrate. A Three-way plus or “dual-bed” converter allows atmospheric air to be injected between the three-way catalyst and an extra oxidation bed to further clean the engine exhaust. Three-way converters are designed to eliminate nitrogen oxides (NOX) as well.

Two-way “oxidation” converters are used up to 1980 and are designed to eliminate hydrocarbons (HC) and carbon monoxide (CO). “Direct-fit” catalytic converters are of three basic types: two-way, three-way and three-way plus oxidation converters. In reality, catalytic converters eventually succumb to contaminants from coolant and engine oil additives and heat stress. Since a catalyst will accelerate a chemical reaction without being consumed by the process itself, the catalytic converter will theoretically last forever.
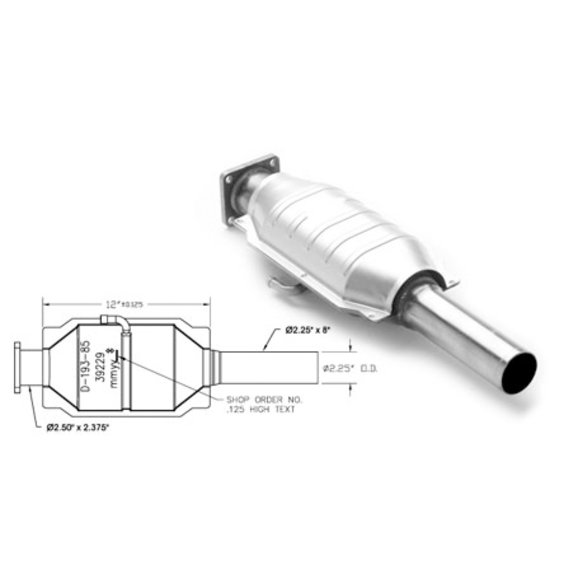
Consequently, a catalytic converter uses precious metals like platinum as a catalyst to convert harmful pollutants like HC, CO and NOX into harmless gases like oxygen (O2), carbon dioxide (CO2) and water (H2O). Unfortunately, a residual quantity of hydrocarbons (HC), carbon monoxide (CO), and nitrogen oxides (NOX) are left over after combustion. An internal combustion engine creates heat energy by igniting a mixture of gasoline and atmospheric oxygen with a high-voltage spark. It’s important to have a basic understanding of how catalytic converters operate when servicing them.
